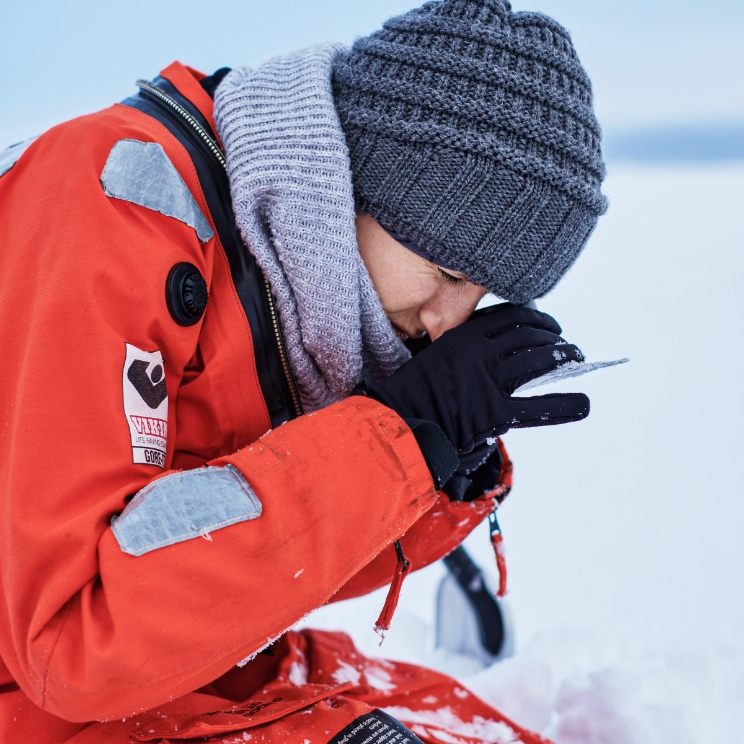
For a better tomorrow
Sea-ice physicist Stefanie Arndt was part of the MOSAiC expedition into the Central Arctic
Read more
The way we work is changing significantly. Careers are becoming less standardized and more individual than in the past. As a global employer with more than 52,000 employees around the world, Boehringer Ingelheim encourages agile and flexible career paths.
Dr. Sven Sommerlatte joined Boehringer Ingelheim as the Head of Human Resources in April 2021. This makes him one of many new employees who joined the company during the COVID-19 pandemic. “One of the many lessons learned from this period is that we can effectively manage the onboarding process virtually,” says the Human Resources expert.
In his role Sommerlatte is responsible for driving the company’s HR processes. In doing so, he must keep two things in balance: On the one hand, the company has to provide its employees with options to make their work as varied and as flexible as possible. On the other hand, it is important to continue the development of the company as a whole.
According to Sommerlatte, this will only be possible “if we invest more time in individual dialogue and less in administration in the future.” The company can only make better personnel and career decisions than its competitors if it gets to know the needs of employees and working partners well and supports their development.
Our office is super cool and I like working here. We love the atmosphere and the lively discussions. None of us here has their own desk, and I adapt my working environment to the working situation. Sometimes I work in the open area, the workshop area, or the product room. If I need to concentrate and avoid distractions, I work in the focus room.
One thing I’m currently working on is an app to help stroke patients regain their life via home-based rehabilitation. It uses an Artificial Intelligence (AI) algorithm to recommend individual rehab concepts and special exercises that are then explained in videos.
We’re working with an international team that is based in different time zones and includes experts from different fields. Under these circumstances, good communication is vital. Our work is very agile – we don’t follow a rigid plan and change direction quickly depending on how the product is. I’m mainly self-taught in this area. I actually learn every day. My area of work requires you to acquire knowledge very quickly. Everything is constantly changing and evolving. That makes our work very exciting.
At that time, I was looking for a way to balance my family, my job, and my hobby. My former supervisor also wanted to work less, but he wanted to keep his managerial position. He asked me if I could imagine the two of us sharing his job. We took this proposal to our supervisors, and we were able to convince them that this could be a good solution.
Each of us got a 60 percent position. One of us worked from Mondays to Wednesdays, and the other from Wednesdays to Fridays. Wednesday was our “alignment day”, where we could discuss important issues.
We both had a very good relationship based on trust. Our guiding principle was that we would complement rather than monitor each other. Our employees, as well as our peers, have appreciated this style of management and cooperation. This requires openness and trust.
For me, the part-time model was the right step at the right time. Of course, you earn less money – but for me, it was worth it. In the second half of 2021, I decided to ramp up and go back to working full-time, to spend more time on my tasks at Boehringer Ingelheim. Following the departure of my job-share partner and former supervisor, I am now in charge of our group.
Fortunately, things are going very well. My apprenticeship covers metalworking and electrical engineering. The apprenticeship has a dual structure, and we rotate between going to vocational school and working at the company. We often attend school from home by webcam, or we work on assignments there. We can try out a lot of things and have lots of room to develop our own ideas.
I prefer to work on-site as much as possible. Working from home permanently wouldn’t be my favorite option, though many of our colleagues are still working remotely. We have the technologies to work well from the site and from home. We connect our laptops to the machines’ user interfaces and can get access from anywhere in the world.
I was particularly fascinated by working in the laboratories under clean-room conditions. I currently work in the production facility of Boehringer Ingelheim’s chemical division. Among other things, I work with highly complex machines that fill little capsules in various production steps.